你現(xiàn)在的位置:主頁(yè) > 彈簧設(shè)計(jì) > 55CrSi鋼閥門彈簧斷裂原因分析
55CrSi鋼閥門彈簧斷裂原因分析
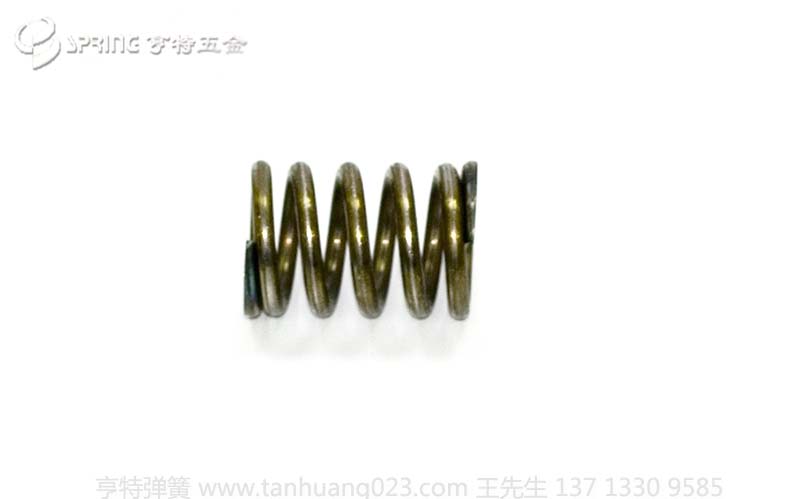
閥門彈簧是各種零部件的重要組成部分,它在閥門關(guān)閉時(shí),確保閥門與閥門座的閉合密封, 閥門開(kāi)啟時(shí),使閥門準(zhǔn)確地隨凸輪運(yùn)動(dòng)。閥門彈簧在工作時(shí)承受周期性交變載荷,由此可以知道閥門彈簧工作環(huán)境惡劣,所受應(yīng)力較大,如果不精心設(shè)計(jì),則閥門彈簧會(huì)過(guò)早的出現(xiàn)疲勞斷裂,一旦閥門彈簧發(fā)生斷裂,將會(huì)引起嚴(yán)重后果,輕則發(fā)動(dòng)機(jī)無(wú)法啟動(dòng),重則會(huì)破壞整個(gè)發(fā)動(dòng)機(jī)。因此對(duì)閥門彈簧進(jìn)行應(yīng)力和疲勞壽命的研究顯得尤為重要。
客戶找到我們,提供了某彈簧廠使用3.6mm55CrSi鋼絲(油淬-回火)繞制成閥門彈簧, 再經(jīng)去應(yīng)力退火、噴丸處理及低溫回火后處理,在進(jìn)行臺(tái)架試驗(yàn)330h后出現(xiàn)疲勞斷裂。為找出斷裂原因,我們對(duì)斷裂彈簧進(jìn)行了理化檢驗(yàn)和分析以解決彈簧壽命問(wèn)題。
1 化學(xué)成分分析
在斷裂彈簧本體上取樣進(jìn)行化學(xué)成分分析,其分析結(jié)果如下:
55Cr Si 鋼絲的化學(xué)成分 (質(zhì)量分?jǐn)?shù))( Chem ica l com position of 55Cr Si steel wire (w t))
條件 |
C |
Si |
Mn |
Cr |
P |
S |
Cu |
標(biāo)準(zhǔn)值 |
0.5-0.6 |
1.2-1.6 |
0.5-0.8 |
0.5-0.8 |
≤.03 |
≤0.03 |
≤0.02 |
試樣 |
0.56 |
1.44 |
0.66 |
0.71 |
0.01 |
0.006 |
0.01 |
2 低倍檢驗(yàn)
將斷裂彈簧用熱酸侵蝕及烘干后用肉眼觀察,可見(jiàn)斷口附近鋼絲表面比較光滑 ,沒(méi)有明顯的裂紋、劃傷 、麻坑和麻面等缺陷存在。裂紋源位于斷口一側(cè)的邊緣 ,并由此向內(nèi)擴(kuò)展 .
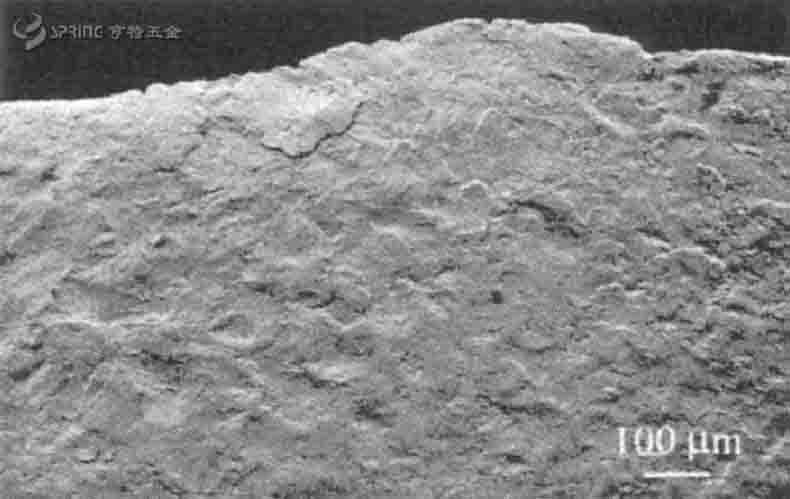
*鋼絲斷口表面形貌(T he fracture appea rance o f the steel w ire)
3 金相檢驗(yàn)
截取斷口處試樣進(jìn)行鑲嵌、研磨和拋光后用4 %硝酸酒精溶液侵蝕 。 在 400 倍光學(xué)顯微鏡下觀察發(fā)現(xiàn)脫碳層 0.01 mm , 未全脫碳 ;
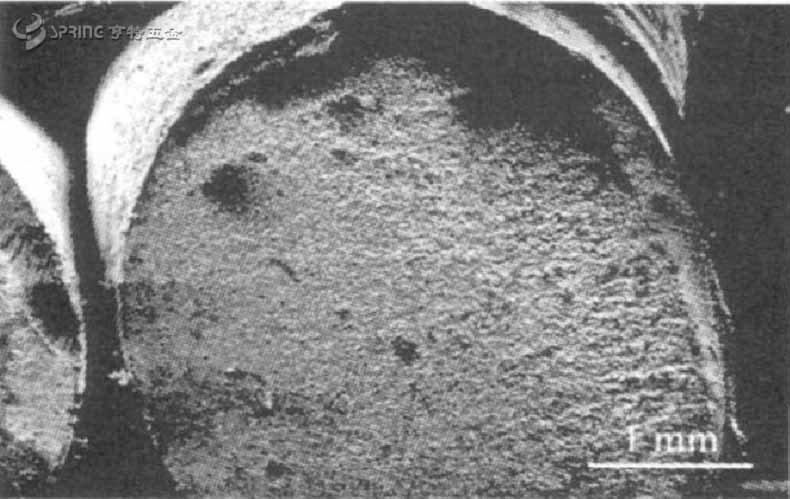
*斷口低倍形貌(Fr actur e appearance in low m ag nificatio n)
顯微組織為回火屈氏體,未發(fā)現(xiàn)異常組織。
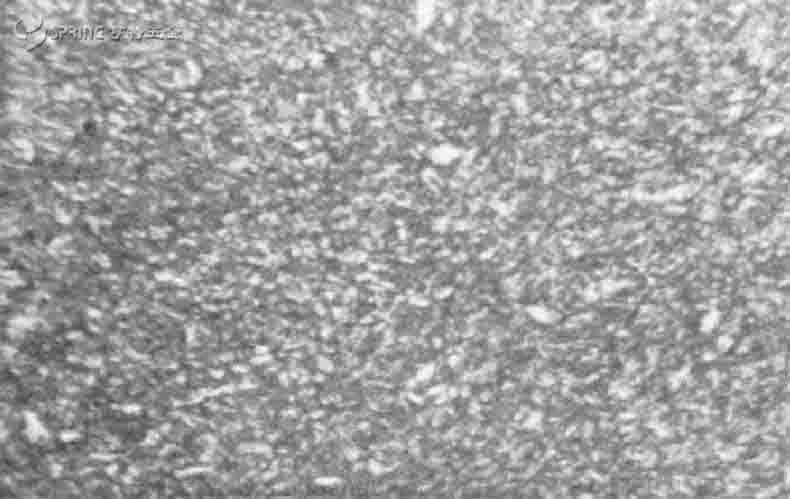
*鋼絲的顯微組織400×(M icrostr ucture o f the steel wire)
4 斷口分析
用掃描電鏡對(duì)鋼絲斷口處進(jìn)行分析, 鋼絲斷口的裂紋源如圖所示, 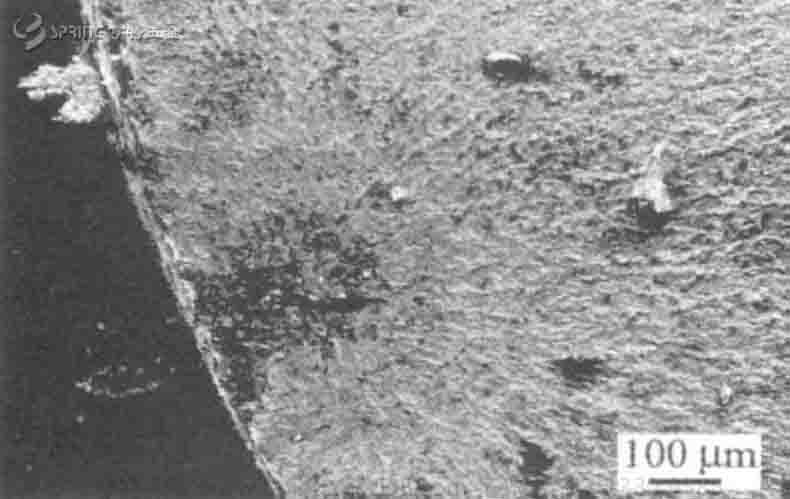
裂紋源(T he cr ack sour ce )
進(jìn)一步觀察發(fā)現(xiàn)裂紋源處存在夾雜物。
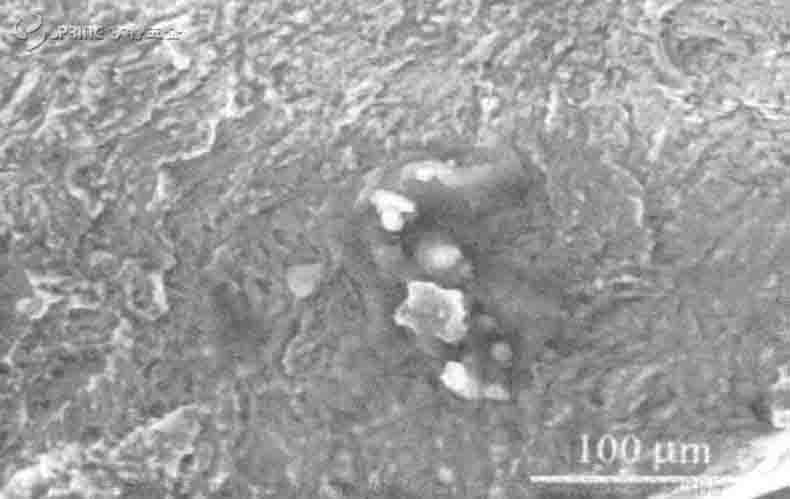
裂紋源處非金屬夾雜物(T he nonm etallic inclusion in the)
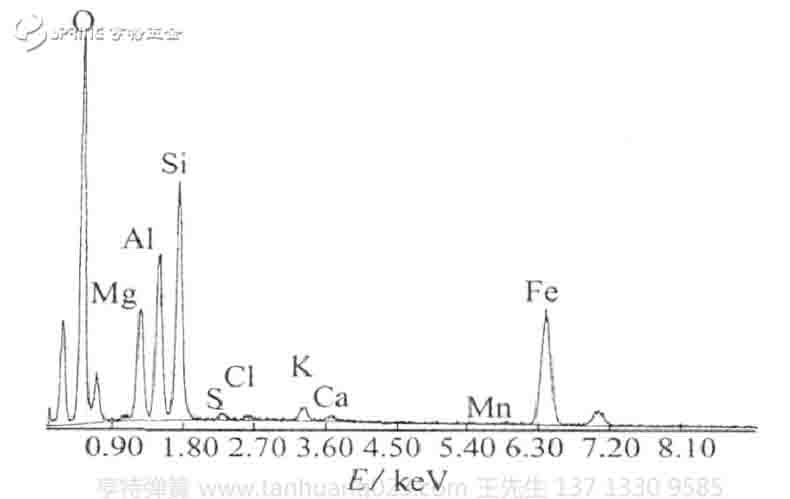
對(duì)夾雜物進(jìn)行能譜分析, 發(fā)現(xiàn)其主要成分為硅 、鋁和鐵, 是夾雜物成分的能譜分析結(jié)果,
AI |
Mg |
Si |
O |
Fe |
K |
S |
11.38 |
8.91 |
15.45 |
36.98 |
24.86 |
1.03 |
0.38 |
夾雜物成分的能譜分析結(jié)果(質(zhì)量分?jǐn)?shù))( Com positio n o f the inclusion by ene rgy spectrum analy sis (w t)) 圖為能譜分析的定量結(jié)果 。明顯可見(jiàn)鋼材中有非金屬夾雜物。
5分析與討論
由于彈簧長(zhǎng)期處于周期性載荷作用下, 要求具有高的疲勞強(qiáng)度、耐沖擊性能和彈性變形能力;此外,彈簧材料對(duì)表面質(zhì)量要求也很高,因?yàn)椴牧媳砻嫒毕菀自斐蓱?yīng)力集中,且表面粗糙度越高,彈簧的疲勞強(qiáng)度也會(huì)越低。55C r Si低合金鋼經(jīng)油淬火-中溫回火后獲得回火屈氏體組織, 可保證彈簧具有高的彈性強(qiáng)度和屈服強(qiáng)度, 同時(shí)又有足夠的韌度和塑性,但要使之具有高的疲勞強(qiáng)度和耐沖擊性能還必須盡量減少鋼中的非金屬夾雜物, 并盡量提高彈簧的表面質(zhì)量。對(duì)鋼絲的化學(xué)成分分析以及斷口的宏觀和顯微組織檢測(cè)結(jié)果可知 :鋼絲的化學(xué)成分和脫碳層均符合標(biāo)準(zhǔn)規(guī)定, 彈簧斷口鋼絲表面沒(méi)有缺陷存在, 熱處理后的組織(回火屈氏體)正常 ,所以該彈簧產(chǎn)生的吸收邊、5d 過(guò)渡金屬以及稀土金屬的 L2, 3 吸收邊 。3d 和 5d 元素的 L 2 , 3 對(duì)應(yīng)的是有很高 X 射線吸收信號(hào)/背景比的類 d 態(tài)價(jià)電子, 所以試驗(yàn)比較容易進(jìn)行。而 4d 元素的能量在 2 ~ 3 ke V 。對(duì)大多數(shù)晶體單色器來(lái)講, 這一能量范圍所對(duì)應(yīng)的入射角接近45°, 這時(shí)單色器輸出的僅是線偏振 X 射線 。 例如 ,在 Rh 的 L2 吸收邊(3 146 e V), 100 %圓偏振入射光經(jīng)過(guò) Si(111)晶體單色器以后偏振度僅剩下 8 %的 M2,3吸收邊對(duì)應(yīng)的能量范圍在 300 ~ 600 e V[ 19]。盡管信號(hào)/背景強(qiáng)度比不太大(一般 4d 過(guò)渡金屬M(fèi) 2 , 3 邊的 XM CD 信號(hào)是過(guò)渡金屬 L2 , 3的 1/ 25), 在當(dāng)時(shí)的試驗(yàn)條件下, 測(cè)量 M2,3吸收邊的XMCD 譜要比 L2,3 邊容易。
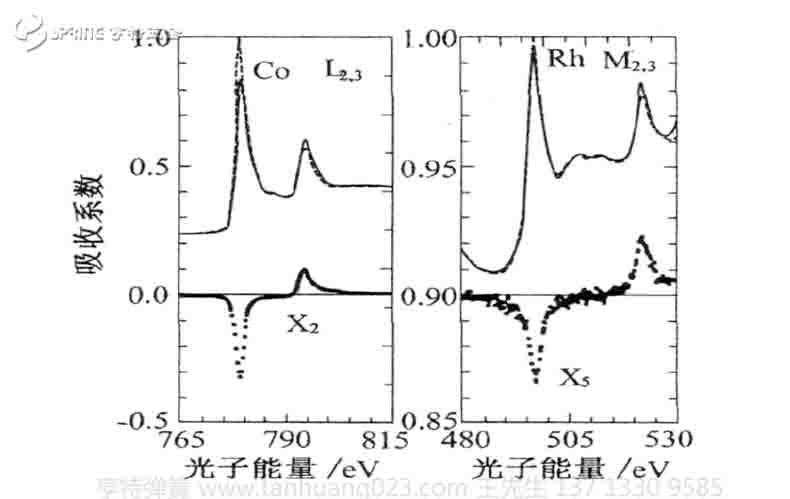
Co0 .77-Rh0 .23合金中 Co L2, 3和 Rh M2 ,3吸收邊的X 射線吸收譜和對(duì)應(yīng)的 X M CD 譜
X-ray abso rptio n spectrum and cor respo ndingXM CD spectrum of Co L2, 3 andRh M 2 ,3 in Co0 .77-Rh0.23alloy
(a) Co L2 , 3abso rptio n side
(b) Rh M2 , 3abso rptio n side
圖中 示出了 Co0.77-Rh0.23 合金對(duì)應(yīng)于 Co L2,3和 Rh M2,3吸收邊的X 射線吸收譜和對(duì)應(yīng)的 XM CD譜。測(cè)量過(guò)程中入射光同樣品表面法線方向成65°。這樣 , 光的偏振方向同樣品的磁化方向分別成25°和 155°。圖中的 X M CD 譜是對(duì)應(yīng)于這兩個(gè)入射角測(cè)得的吸收譜之差, 非零的結(jié)構(gòu)對(duì)應(yīng)于吸收邊的XM CD 結(jié)構(gòu) 。 改變組分后 , 發(fā)現(xiàn) Co0 .49 Rh0 .51 的XM CD 信號(hào) 明顯 減小 。 在 另一 個(gè) 相似 的材 料Co 0 .75 Ru0 .25 上卻沒(méi)有觀測(cè)到 Ru 元素的 M2 , 3 吸收邊的 XM CD 峰 。研究表明 XMCD 效應(yīng)同材料的飽和磁化強(qiáng)度以及剩余磁化強(qiáng)度的大小有關(guān)。比如Co 0 .75 T u0 .25 有較小的磁化強(qiáng)度 , 剩余磁化強(qiáng)度為5 2 %, Co0 .49 Rh0 . 51 的剩余磁化強(qiáng)度僅為40 %, 而51 的剩余磁化強(qiáng)度僅為40 %,而Co0 .77 Rh0 .23 達(dá)到 66 %。疲勞斷裂并不是由于化學(xué)成分、鋼絲表面的宏觀缺陷或者不正常熱處理組織造成的。
由斷口分析可知 :疲勞裂紋起源于鋼絲表層, 彈簧斷口疲勞裂紋源處存在非金屬夾雜物 。由上圖可知,該夾雜物主要是含硅酸鹽和氧化鋁的復(fù)雜氧化物,其中氧化鋁類夾雜物具有高硬度和高熔點(diǎn) ,無(wú)塑性,屬脆性?shī)A雜物,且該夾雜物處于受交變應(yīng)力較大的鋼絲表層。在進(jìn)行臺(tái)架試驗(yàn)的過(guò)程中, 金屬基體發(fā)生彈塑性變形 ,而氧化鋁類夾雜物不能隨基體同步變形,在夾雜物與基體之間形成微裂紋,而微裂紋在循環(huán)載荷的作用下繼續(xù)擴(kuò)展并最終導(dǎo)致了彈簧的疲勞斷裂 。
3 結(jié)論
鋼絲表層存在的脆性非金屬夾雜物是造成彈簧壽命不足的主要原因。
為您推薦其它類似文章:
閥門彈簧
閥門彈簧斷裂
閥門并聯(lián)雙彈簧
閥門彈簧材料
空氣閥門彈簧